PROCESS
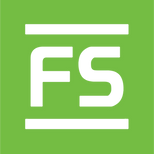
STEP 1: DESIGN AND PLANNING
All FiberSprung floor designs are based in Computer Aided Design (CAD). These designs are manufactured from the CAD files to quality tolerances defined by drawings. This ensures consistency for all FiberSprung parts within our floors. Below is a 3D rendering of the FiberSprung Go floor.

When an order for a floor comes in, the floor is laid out in CAD, from architectural drawings, manual measurements, or digital scans.
​​
Pre-planned layouts ensure lean efficiency, less waste, and cost savings in time and materials for FiberSprung and our customers.
​​
These drawings inform for purchasing the optimal quantities of materials, and also gives a plan to the FiberSprung installation team on site how to build the floor.

STEP 2: THE FIBERGLASS GRID
The grid is the first step to build a FiberSprung floor. It is the fiberglass basket-weave support structure of the FiberSprung Pro and Light floors. The fiberglass matches the bend characteristics of the classic wooden sprung floor, with much more consistency.
​​
At FiberSprung, we believe in sustainability. The materials within the fiberglass grid are specifically chosen to have an over 30 year use life, and the floor is designed to be easily repaired. Sadly, water damage happens in studios sometimes, and it's no one's fault. Our grids are designed to withstand even a flood.
​
FiberSprung stands by our fiberglass grid design with a 20 year warranty, and offers services to help our customers relocate or even resell their floors if needed. ​​​
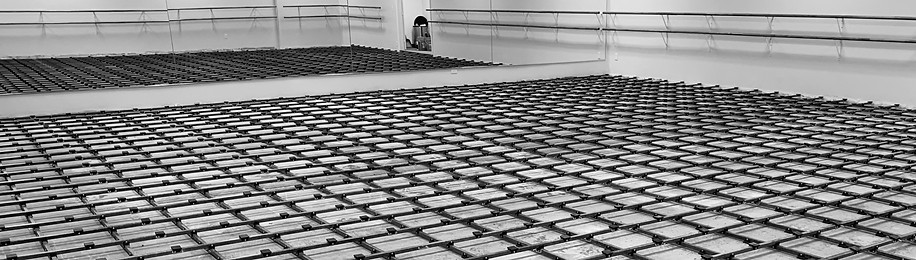
Bend Testing:
For science, we bend tested the wood of a wooden sprung floor versus our Pro floor fiberglass, which was designed to exactly mimic its bend characteristics. ​​​​​​​We tested 10 support beams, from two different suppliers, made of 1x4 pine (a wood which is typically used in these floors). We found a 3ft span to bend between 3mm to 7mm, depending on the grains of the wood. Sometimes, we even found one side of the wood to bend more than the other. Our fiberglass bent 3mm every single time. (with samples from two different suppliers)

STEP 3: THE SUPPORT SURFACE
FiberSprung uses a 1 layer plywood surface made of 3/4" or 1" plywood. At each joint between two pieces of plywood, the edges are tongue-and-grooved together. To further support the joint, each side of the joint is fastened to a fiberglass plate. This supports both sides of the plywood, and results in a homogenous-feeling support surface.
​
FiberSprung customer support begins with great design. We have chosen to focus on having single layer plywood designs for extreme ease of repair and service. This allows us rapid repair and the most options during a stressful situation if a floor is unfortunately damaged.

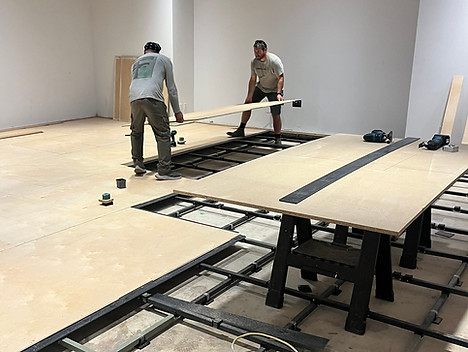
STEP 4: THE PERFORMANCE SURFACE
The plywood support surface is typically covered with marley for dance. Other than marley, there are other options such as thin engineered hardwood or vinyl flooring. The finishing touch of our service includes installing the floor surface for our customers.

THE GO FLOOR:
The FiberSprung Go floor is a single layer sprung floor. It uses one layer of fiberglass, fastened to the bottom of 4' x 4' plywood boards, to provide the bend required in the floor. The boards tongue and groove together like the regular floors; but rather than fastening to fiberglass supports. It is assembled using mechanical locks which are activated using one tool: an 8mm hex wrench.
